The evolution of the manufacturing sector has continuously surprised industries worldwide, and the TI02 powder factories represent a quintessential example of this progression in high-tech production. Constantly advancing in both technological prowess and environmental considerations, these factories are setting new standards for quality and sustainability within the industrial landscape.
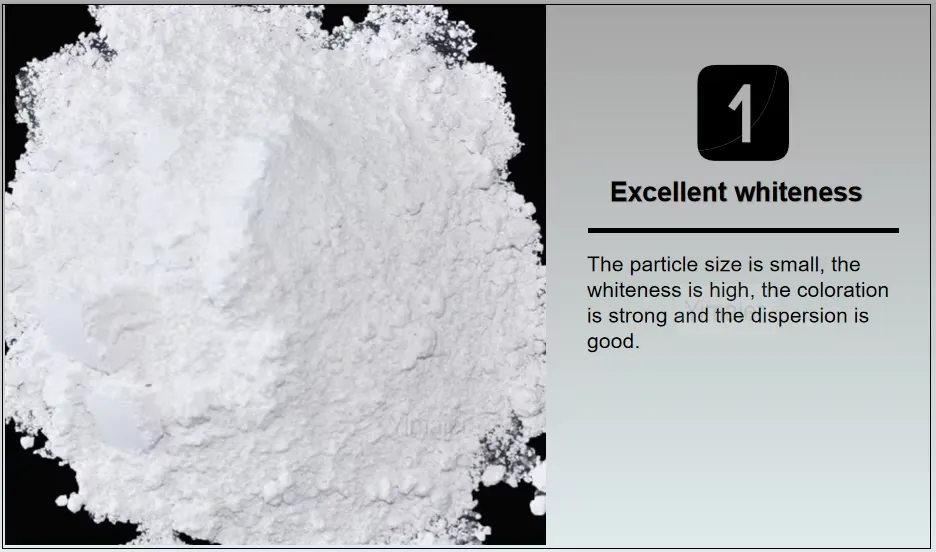
Titanium dioxide, commonly referred to as TiO2, is a critical component in various product categories ranging from paints and coatings to cosmetics and even food items. Its widespread application speaks to its versatility and importance across diverse sectors. However, the complexities involved in its production are often underestimated.
Let's dive into the specificities that define the modern TiO2 powder factories.
Experience in TiO2 Powder Production
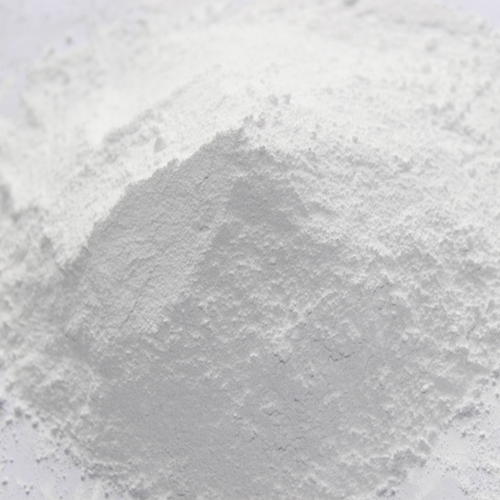
Navigating the intricacies of TiO2 production requires extensive experience and understanding of the material's nature and its applications. Veterans in this realm highlight that the production process often begins with the meticulous selection of raw materials. Only high-purity titanium ore, such as ilmenite or rutile, is used to ensure the quality of the end product.
Factories with a history of excellence in TiO2 production emphasize employing cutting-edge processing techniques to extract and purify titanium compounds effectively. These manufacturing units utilize advanced technologies like the sulfate and chloride processes, tailored to maximize efficiency and yield. The choice between these methods often depends on the desired application of the TiO2, illustrating the manufacturer's depth of expertise and experience in selecting the optimal approach.
Expertise in Advanced Manufacturing Techniques
The modern TiO2 manufacturing process involves distinct stages that require specific expertise, from raw material handling to finishing. Each step, including ore preparation, digestion, purification, and crystallization, demands precision and a high degree of technical know-how. Factories on the leading edge invest significantly in research and development to refine these processes continually. Innovations such as improved kiln designs and enhanced filtration systems not only boost production efficiency but also minimize environmental impact, showcasing a blend of technical expertise and ecological responsibility.
Moreover, implementing state-of-the-art quality control systems ensures that each batch of TiO2 powder maintains consistent quality. Advanced spectrometry and automated testing methods allow for precise monitoring, avoiding any impurities that may affect performance. This level of sophistication in quality assurance reflects a factory's authoritative stance in the industry.
ti02 powder factories
Authoritativeness and Industry Standards
TiO2 factories that stand out in authority frequently align themselves with industry standards and regulatory compliances, often exceeding norms to set benchmarks. Active participation in global forums and collaboration with regulatory bodies underline their commitment to maintaining and elevating production standards. Leaders in the field are also proactive in publishing research papers and contributing to industry white papers, solidifying their role as trailblazers.
These factories often possess an extensive portfolio of patents, displaying their dedication to innovation and advancement. The development of novel TiO2 formulations that enhance performance characteristics such as UV resistance and opacity are testaments to their pioneering research efforts, reinforcing their authoritative position within the industry.
Trustworthiness Through Sustainable Practices
Modern TiO2 powder factories prioritize sustainable manufacturing practices, seeking to mitigate their environmental impact. Conscious of the ecological ramifications, these manufacturers invest in renewable energy sources and waste reduction strategies. The implementation of closed-loop systems and recycling initiatives demonstrates their commitment to minimizing carbon footprints and conserving resources.
Trust is further built through transparency and consistent communication with stakeholders, including customers, suppliers, and the local community. Open disclosure of environmental performance data and the pursuit of third-party certifications, like ISO 14001 for environmental management, reflect a dedication to trustworthiness and ethical operations.
In conclusion, the evolution of TiO2 powder factories encapsulates a commitment to quality, innovation, and sustainability. With robust experience, technical expertise, authoritative industry presence, and a foundation of trust, these manufacturing units are not merely purveyors of TiO2 but innovators shaping the future of material production. As the demand for high-quality, sustainable products surges, TiO2 powder factories continue to exemplify excellence in the industrial sector.