In the competitive landscape of manufacturing, the integration of innovative materials has become crucial for enhancing product quality and meeting evolving industry standards. Among these materials,
titanium dioxide has emerged as a key component for nitrile glove manufacturers. Its unique properties not only elevate the overall quality of the gloves but also contribute to improved safety and durability, offering a competitive edge in the marketplace.
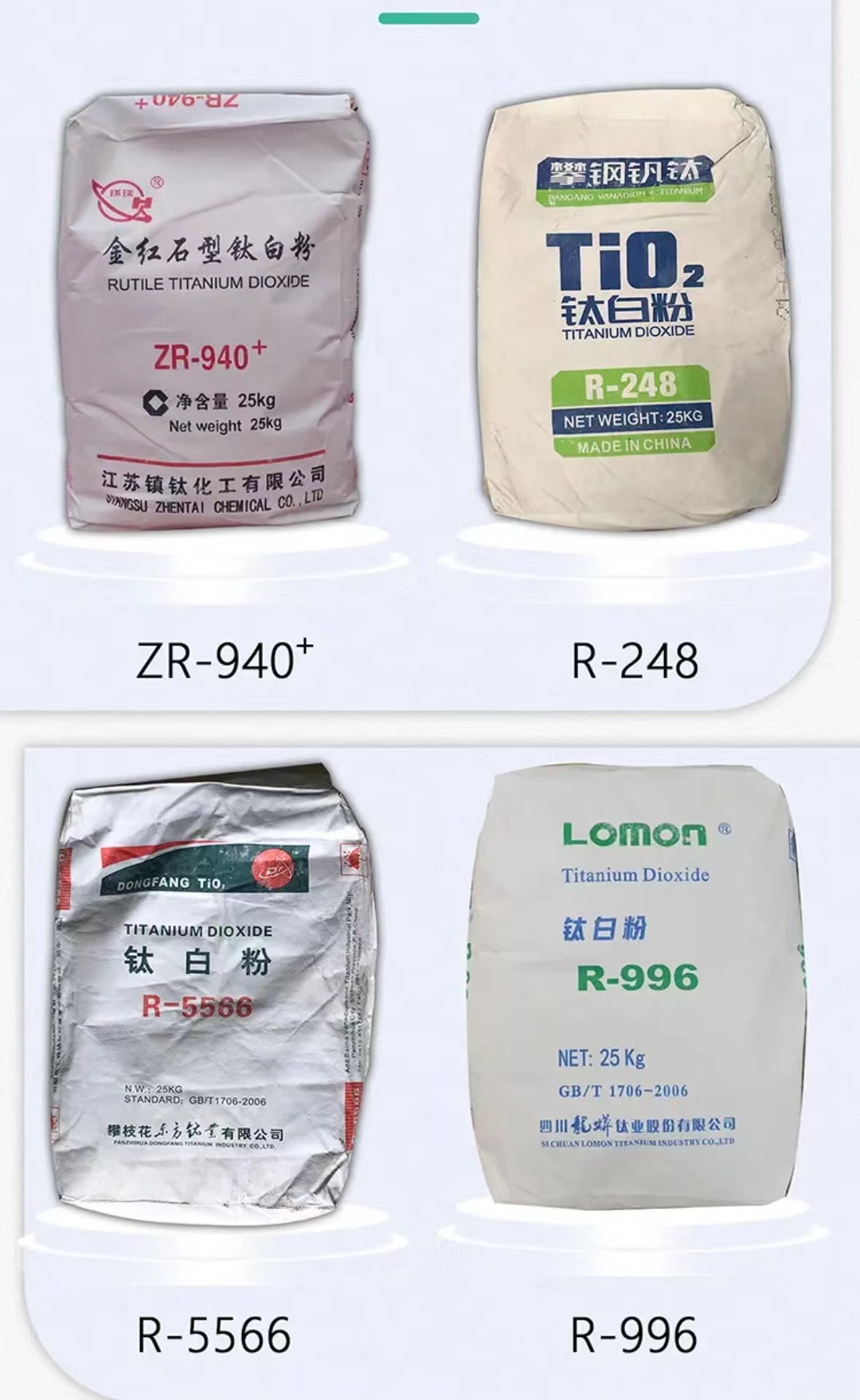
Titanium dioxide is renowned for its exceptional chemical stability, high refractive index, and bright white pigmentation, making it an ideal additive for nitrile gloves. The inclusion of titanium dioxide in the glove manufacturing process enhances opacity, which is essential for aesthetic appeal and identifying visible defects in the gloves post-production. This improvement in visual quality can be pivotal for manufacturers aiming to differentiate their products in a market where first impressions count.
Expert experience in utilizing titanium dioxide includes a profound understanding of its interaction with nitrile butadiene rubber (NBR), the core material for nitrile gloves. By uniformly distributing titanium dioxide particles throughout the glove, manufacturers can achieve consistent performance in terms of elasticity and tensile strength. This uniformity is crucial as it ensures that each batch of gloves meets stringent quality control standards, thereby reinforcing credibility and trust within the supply chain.
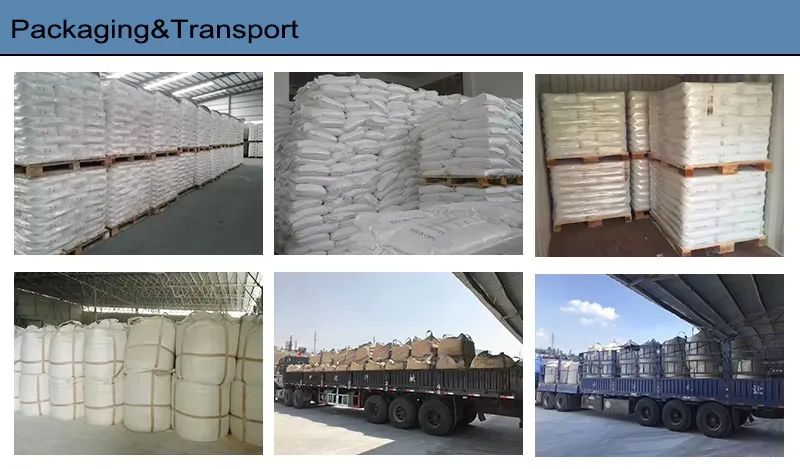
Furthermore, the expertise in balancing the amount of titanium dioxide is essential; too little might undermine the benefits, whereas too much can impact the glove’s texture and flexibility. Manufacturers with authoritative knowledge in this domain can optimize the formulation, enhancing the durability and longevity of the gloves without compromising tactile sensitivity, which is critical for end-users in fields requiring precision, such as healthcare and pharmaceuticals.
titanium dioxide for nitrile gloves manufacturer
From an authoritative perspective, the incorporation of titanium dioxide is also influential in enhancing the glove's resistance to UV radiation and other environmental factors, thereby extending shelf life and usability. This aspect not only meets the demand for durable products but also aligns with the growing trends towards sustainability and waste reduction in manufacturing practices.
Trustworthiness in this context is underpinned by compliance with international standards and certification processes, which are pivotal in a regulated industry. Successful manufacturers adept at integrating titanium dioxide into their production can showcase adherence to ISO standards or FDA guidelines, thereby reinforcing their position as reliable suppliers in the global market.
In conclusion, the strategic use of titanium dioxide in nitrile glove manufacturing is a nuanced process that demands a blend of experience, expertise, and a strong commitment to quality and regulatory standards. As manufacturers continue to explore innovative materials to enhance product offerings, titanium dioxide remains at the forefront, ensuring that products not only meet but exceed consumer expectations for safety, performance, and sustainability. This commitment to leveraging advanced materials and maintaining rigorous standards will undoubtedly position manufacturers as leaders in the production of high-quality, reliable nitrile gloves in an increasingly competitive landscape.