Investing in a titanium dioxide plant can be a game-changing move for manufacturers and industrialists seeking to dominate the additive market. As an essential component in producing paints, coatings, plastics, and even cosmetics, titanium dioxide offers unmatched opacity and brightness. With roots tracing back to its discovery in 1791, the material has become a critical element in industrial applications worldwide. Setting up a titanium dioxide plant requires an understanding of cutting-edge technologies, regulatory standards, and market demands, all of which ensure the product meets the high expectations of various industries.
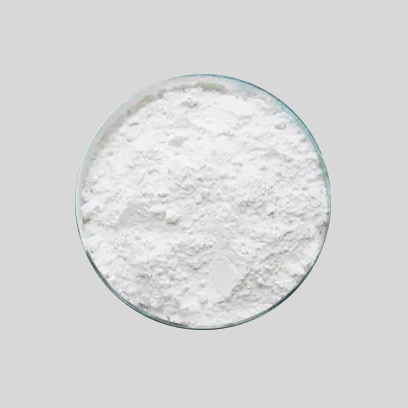
To begin with, the location of a titanium dioxide plant is crucial. Proximity to the raw materials like ilmenite or rutile ores, essential for production, drastically impacts operational costs and logistical efficiency. Furthermore, the site should accommodate sustainable practices, as eco-compliance is a significant factor today, given the environmental regulations aimed at reducing carbon footprint in production processes.
Technological expertise is imperative in the operation of a titanium dioxide plant. The Chloride Process and Sulfate Process are the two primary methods of production, each with distinct benefits and challenges. The Chloride Process, favored for producing higher-grade titanium dioxide, demands a more significant initial investment as it involves handling hazardous chemicals like chlorine gas. On the other hand, the Sulfate Process is less capital intensive but generates a substantial amount of waste, necessitating efficient waste disposal systems to meet environmental standards. Operators need a thorough understanding of these processes to optimize production and maintain quality control throughout.
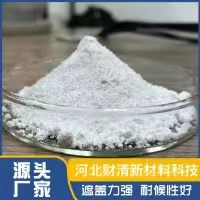
Quality assurance cannot be overstated in titanium dioxide production, with its applications requiring a high degree of purity and consistency. The implementation of rigorous quality checks and on-site laboratories ensures the product adheres to international standards. These quality protocols bolster the plant's reputation and foster trust among clients and partners — a non-negotiable in maintaining industry competitiveness.
titanium dioxide plant
A titanium dioxide plant’s success hinges on regulatory compliance. Authorities such as the Environmental Protection Agency (EPA) in the United States and the European Chemicals Agency (ECHA) have stringent guidelines to ensure environmental and occupational safety. Compliance with these regulations not only enhances the plant's credibility but also opens up global markets by meeting import standards.
Entwined with expertise and compliance is the continuously evolving market landscape that demands constant innovation. A plant's adaptability to market trends, such as the rising demand for sustainably produced and low-carbon footprint titanium dioxide, can significantly impact its market share. Investing in research and development paves the way for innovation in production processes and the development of new product grades tailored to meet specific industrial needs, fortifying the plant's market positioning.
Trustworthiness remains a pivotal attribute that can make or break a business venture. Building long-lasting relationships with reliable suppliers and clients is essential. This includes transparent communication, consistent product quality, and an unwavering commitment to ethical standards. Establishing a brand known for these qualities creates a sustainable business model that attracts repeat business and referrals.
In conclusion, setting up a titanium dioxide plant is not merely about manufacturing but about embodying expertise, compliance, market insight, and trust. Recognizing the intricacies of the industry and aligning with best practices catapults a manufacturer to the forefront of this competitive and ever-changing market, promising growth and long-term success.