TiO₂, commonly known as titanium dioxide, is a versatile compound that finds application in multiple industries, predominantly in manufacturing, cosmetics, and food. Factories dedicated to producing titanium dioxide have become crucial in supporting these sectors due to the compound's unique properties like exceptional whiteness, high refractive index, and UV-resistant capabilities.
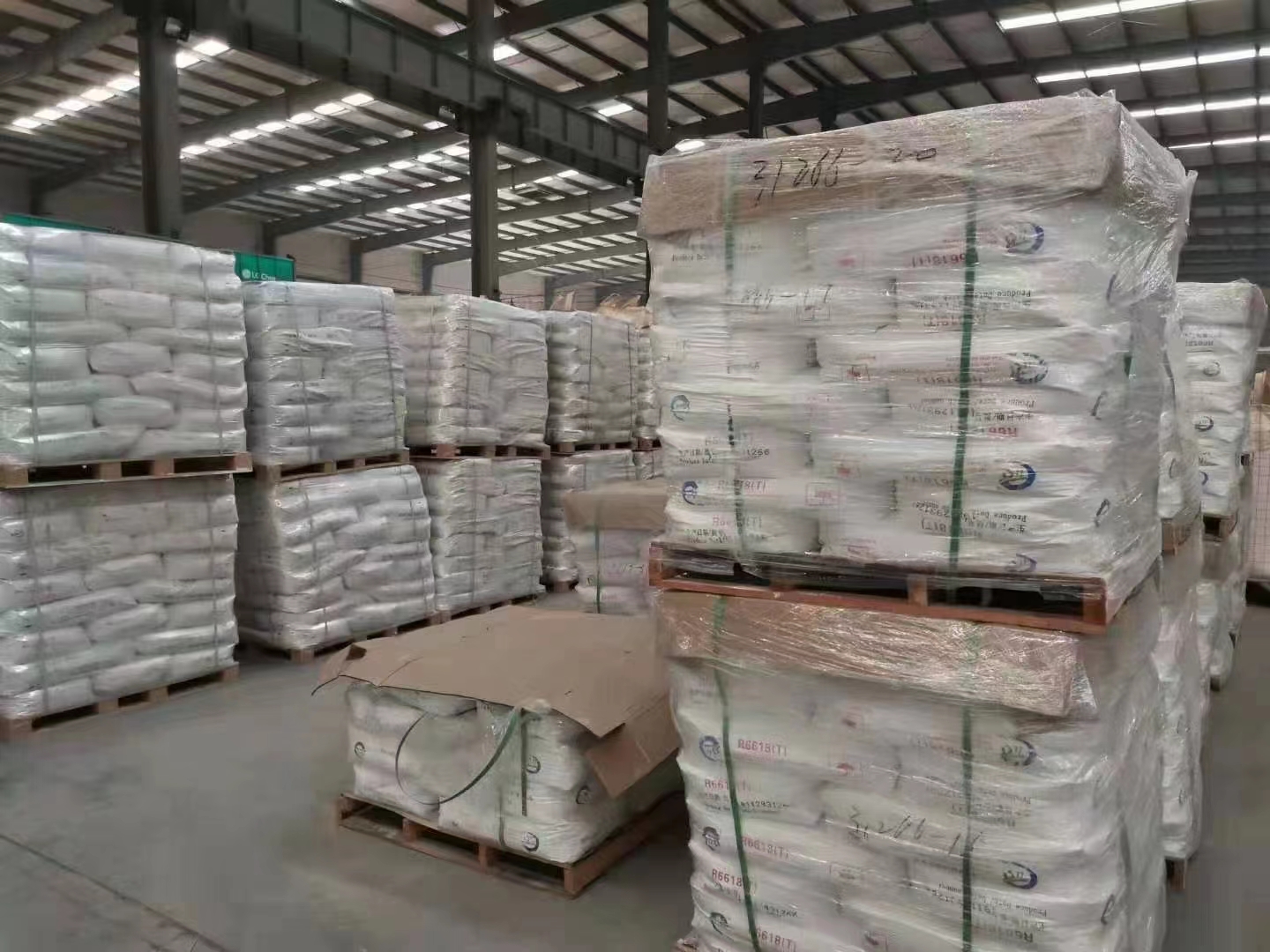
Initially launched in the early 20th century, titanium dioxide production has evolved significantly. The modern titanium dioxide factories are now equipped with advanced technology that emphasizes efficiency, sustainability, and safety, crucial parameters in the 21st century. These factories predominantly utilize two processes for TiO₂ production the sulfate process and the chloride process. Each method comes with its unique set of advantages and environmental considerations.
Through extensive research and development, factories employing the sulfate process have optimized it for producing anatase and rutile forms of titanium dioxide. The sulfate process, though traditional, is advantageous for its ability to use a range of ilmenite ores as feedstock and produce diverse TiO₂ grades that fit various applications, from paints to paper manufacturing. The process's waste management systems have substantially advanced, reducing its environmental footprint, a critical concern for communities and policymakers.
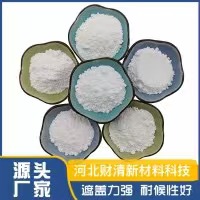
On the expertise front, factories using the chloride process offer high purity TiO₂, crucial for industries demanding premium quality, such as the automotive and aerospace sectors. This method, which uses chlorine gas to obtain titanium tetrachloride, emphasizes a closed-loop technique that recycles byproducts, minimizing waste. Expertise in handling chlorine safely ensures these factories achieve a reduced environmental impact, prioritizing worker safety and surrounding ecosystems' health.
Authoritativeness in titanium dioxide production stems from regulatory compliance and innovation in product applications. Leading factories adhere rigorously to global standards, such as those set by ASTM International and the International Organization for Standardization (ISO). By engaging in collaborative research initiatives, these factories stay ahead in developing new TiO₂ applications and ensuring the compounds align with future technological advancements, like photovoltaics and energy storage.
titanium i oxide factories
Trustworthiness in the titanium dioxide industry is vital. Thus, leading factories maintain transparency in operations and product offerings. Sustainable practices, like the circular use of waste byproducts and significant reductions in carbon emissions, showcase these factories' commitment to environmental and social responsibility. Engaging with communities through educational workshops and partnerships amplifies their societal contributions, ensuring the equitable growth of associated regions.
The titanium dioxide industry is undergoing a transformative phase, incorporating artificial intelligence and machine learning in manufacturing processes. These technologies enhance predictive maintenance, reduce production downtime, and optimize energy consumption, contributing to superior quality control and operational efficiency. Factories that integrate these advancements substantiate their authority as pioneers, maintaining a competitive edge while promoting sustainable practices.
Moreover,
global collaboration among titanium dioxide-producing factories is pivotal. Sharing knowledge on best practices and technological innovations fosters a sense of community, where collective expertise helps address industry-wide challenges, such as regulatory changes and fluctuating demand dynamics. These collaborations often lead to the development of enhanced TiO₂ products with tailored properties, meeting specific customer needs more effectively.
In conclusion, titanium dioxide factories stand at the crossroads of innovation, sustainability, and functionality. Their evolution is propelled by an unwavering commitment to refining production techniques and exploring novel applications, thus underpinning numerous industries. As demand for TiO₂ surges, these factories will continue to adapt, embodying resilience and foresight in an ever-evolving global marketplace. Whether through meticulous adherence to environmental practices or technological integration, titanium dioxide factories are pivotal in shaping a sustainable and progressive future in materials production.